Metal Sheet Bending Machine
A Metal Sheet Bending Machine is a heavy duty and precise machine for bending or curving metal sheets into your desired shape. The machine is used in industries such as automobile, construction and manufacturing where precise and fast metal fabrication is needed. In plain terms a metal sheet bending machine is utilized for fabrication of metal parts such as brackets, enclosures and panels by bending and shaping metal sheets. The machine consists of extremely strong hydraulic or mechanical motors to provide sufficient force to bend metal with high accuracy. Some of the installations also accommodate sheet thicknesses, angles etc. varying so it provides lot of flexibility and versatility for modifying production needs. This machine is made with strong construction and good quality material for durability and less maintenance. With this user-friendly interface, the operator can effortlessly control the metal bending machine and select the proper procedures and adjustments to ensure high output quality. The metal sheet bending machine is a secure working place, and with safety features like emergency stop switches and safety covers, both the machine and the operator are protected properly. For some great deals on high-quality metal sheet bending machines, check out Aajjo.
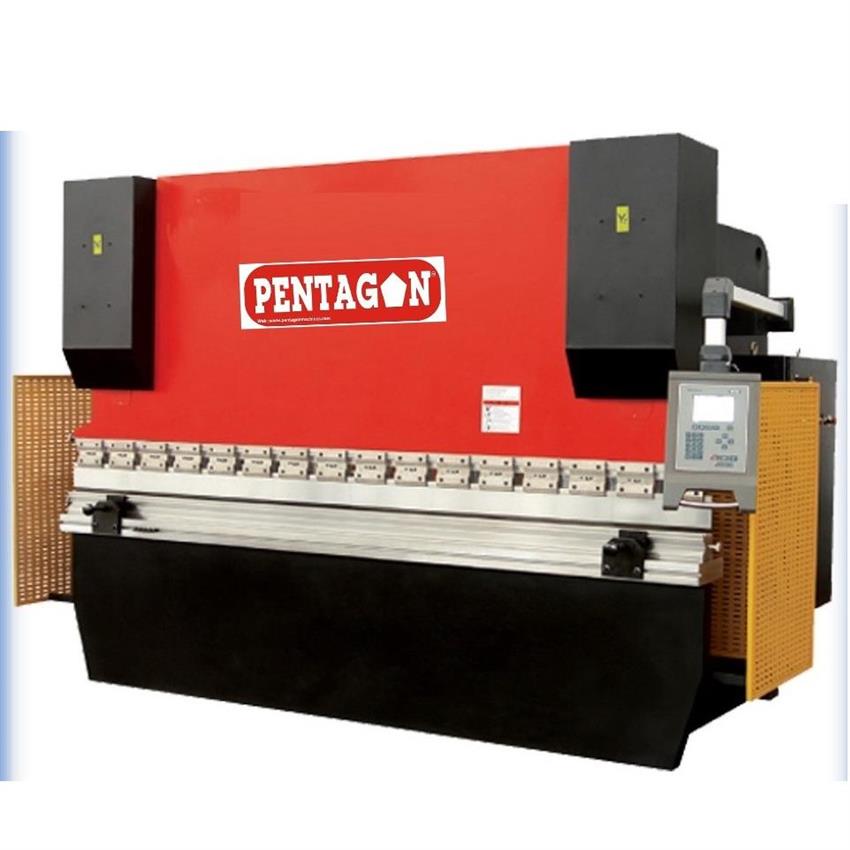
Hydraulic NC Press brake model WC67Y 200T/6000 mm
₹
3,055,000.00
₹3,162,000.00
General Details: | |
Model | WC67Y 200T/6000 |
Automatic Grade | yes |
Sheet Material | mild steel |
Material | steel |
Usages | Sheet metal bending |
Others: | |
Distance between columns (mm) | 4800 |
Main motor power (kw) | 15 Kw |
Max. Shut Height (mm) | 460 mm |
Nominal pressure (kN) | 2000 |
Packing Size (LXWXH in mm) | 6500x1950x3300 mm |
Slider stroke (mm) | 200 mm |
Strokes per min | =6 |
Throat depth (mm) | 350 mm |
Weight of machine | 21000 Kgs |
Workbench length (mm) | 6000 |
NC Press brakes:
Main feature
1. The frame is steel structure, left and right vertical plate, table and pressure plate welded into a unitary structure, after welding to eliminate internal stress by tempering, exceptional rigidity, high stability.
2. Important parts of the frame, sliders, etc. are used ANSYS finite element analysis software to ensure machine reliability.
3. Hydraulic drive, cylinder on both end of machine, disposed on the slider to drive it work directly.
4. Torsion axis synchronization for slide synchronous mechanism.
5. Adopt a mechanical stopper mechanism, stable and reliable.
6. Back Gauge size and slide stroke controlled by NC system, back gauge with high precision ball screw, stable operation and precise positioning.
7. The NC system adopts frequency conversion control technology, with multi-step
programming function, simple and easy to operate.
8. Inclined wedge deflection on the compensation mechanism, in order to guarantee access to high bending accuracy
Safety barrier device all around the machinery, electrical cabinets equipped with Open door cut-off function, emergency stop button around front and back, protective cover foot switch to ensure safe working
Steel-welded frame, vibration to eliminate stress, with high strength and good rigidity. Hydraulic top-drive, steadiness and reliability.
Hydraulic top-drive, steadiness and reliability. mechanical stop steel torsion bar to maintain synchronization, high precision.
Motorized-adjusting device of backgauge and rams stroke, fine adjusting by handwheel, numerical display.
Deflection compensation unit installed on the top die. Manual crowned bottom die holder is adopted for the machine above 250ton length 4000mm. Travel limit protection, full machine guarding with safety interlocker
Performance characteristics
1. Multi-language NC operating system
2. Silent and reliable internal gear pump
3. Hydraulic system regulated by proportional valves
4. Combination of brushless drive and motor with "can open" digital technology, high precision backgauge which permits permits fast movements of the axes.
5. High precision optical lines
6. Adjustable clampings
7. Hardened, grinded tools and clamps for quick tools adjustment
8. Complete backgauge fingers on double linear guide
9. Stainless steel front supports adjustable in height
10. Automatic/mechanical crowning
11. Electrical panel with high quality components
12. European safety standards Start&Stop system
Delivery: 30-40 days from the date of PO along with advance but we keep these machines in stock and will be confirmed exact delivery schedule at the of order finalization
One Year against any manufacturing defect
Tell us your Requirement
if you are interested, please fill the below details: